Stick Fly
Stick Fly was the eighth show in the UNCSA 2019-2020 season and was performed in Patron’s Theatre. The process for Stick Fly was a long one, it’s greenlight process started on November 4th and went through November 15th. Engineering time began the following Monday, November 18th, and went until build started on December 9th. Build was somewhat disjointed though as the first week of build was Intensive Arts and as such was a 40hr work week. following that though we went on winter break and did not return until January 13th; Build continued from that point until January 30th. Load in for the show was initially only seven days, February 1st-7th, but was expanded to nine, January 29th to February 7th. There were six days of tech, February 7th-12th, followed by two weeks of runs with strike being on February 23rd & 24th.
Stick Fly primarily had problems attached to phases rather than one overarching problem to be overcome. During greenlight the problem was that the initial design came in at 265% of the initial budget. It took three meetings post the first to bring the bid in line with the budget given for the show. This was achieved by coming to each meeting with an updated list of what things cost, what percentage of the budget it was, and what percent of the scenery it was. This information was then presented to the Scenic Design team and what could change, what could be reworked, and what would be cut was discussed. Once that was settled the engineering began. In engineering the problem that most stood out was how to deliver the high level of finish asked for by the play/designer with a crew inexperienced in construction let alone finish construction. I did as much as I could to limit this by keeping the skeleton of the set as simple as possible. To cite some examples. All walls were square shaped until they could no longer be and then a custom piece would be bolted to the standard shaped ones, all easy walls were built first to give the crew experience with tools and expectations before continuing to the harder ones. The build period had the expected and usual problems to it such as misread drawings, miscut materials, and below acceptable quality pieces. All of this was combated by clear face to face communication, paying attention, recycling material, and in some cases disassembly followed by reconstruction after discussing what was wrong. Originally the wall for load-in was going to be the very small period to do it, but once the window was extended it became more of making sure the sequence we did things in was correct. Following that just making sure to hit the obvious cracks in the scenery that would break suspension of disbelief and making sure everything was nice was the goal. Similar to load in, load out was primarily a question of what sequence things went out in and how much can fit into a truck.



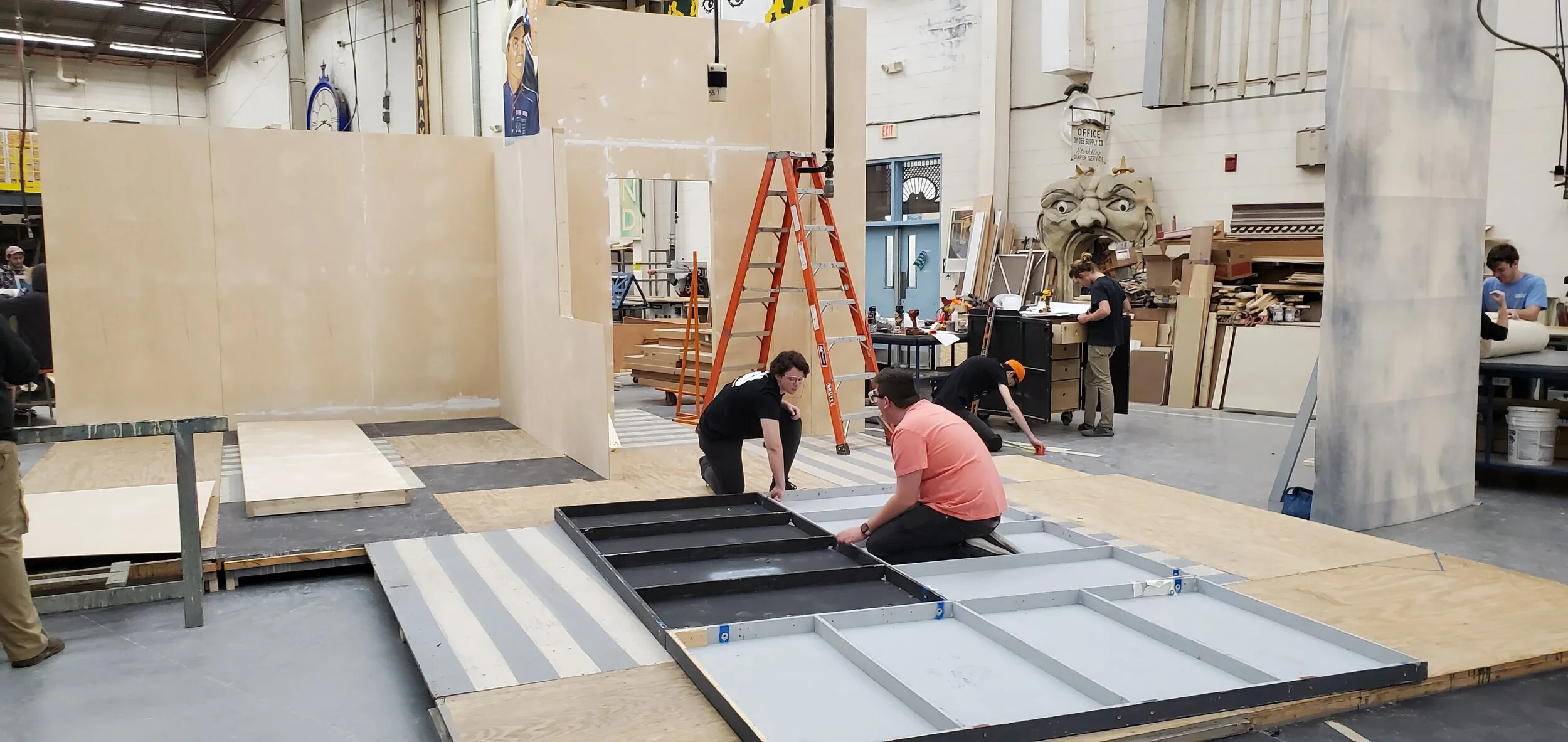

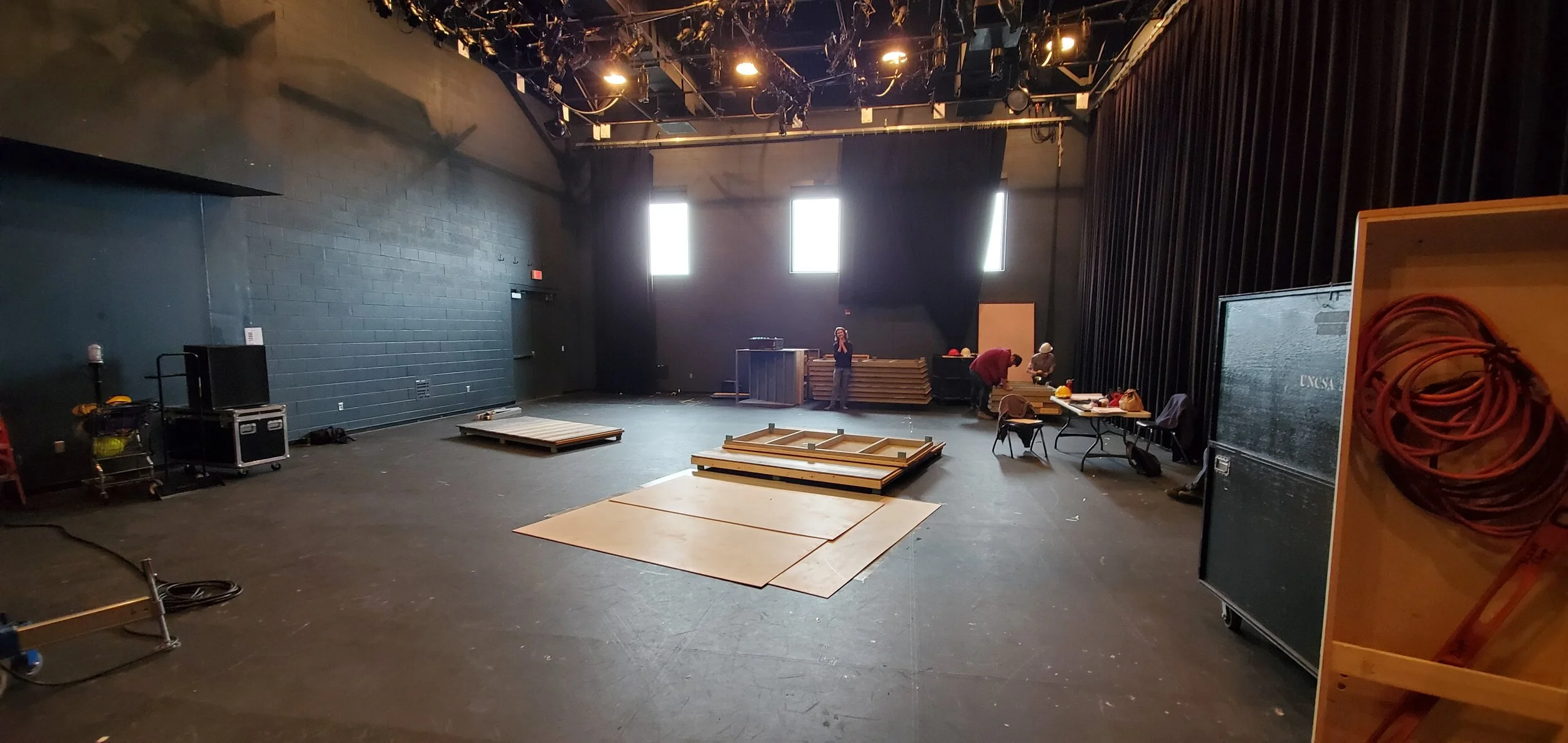






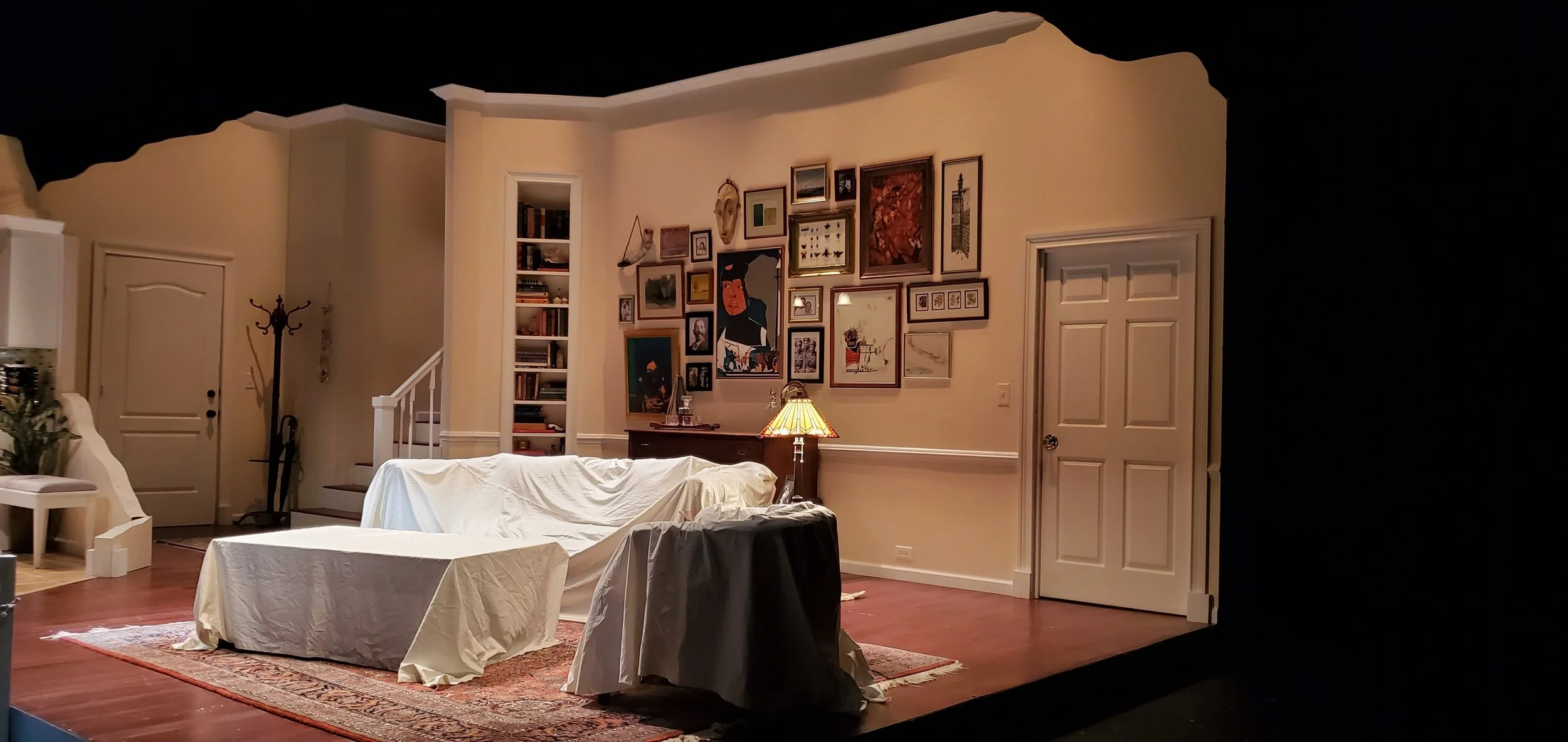

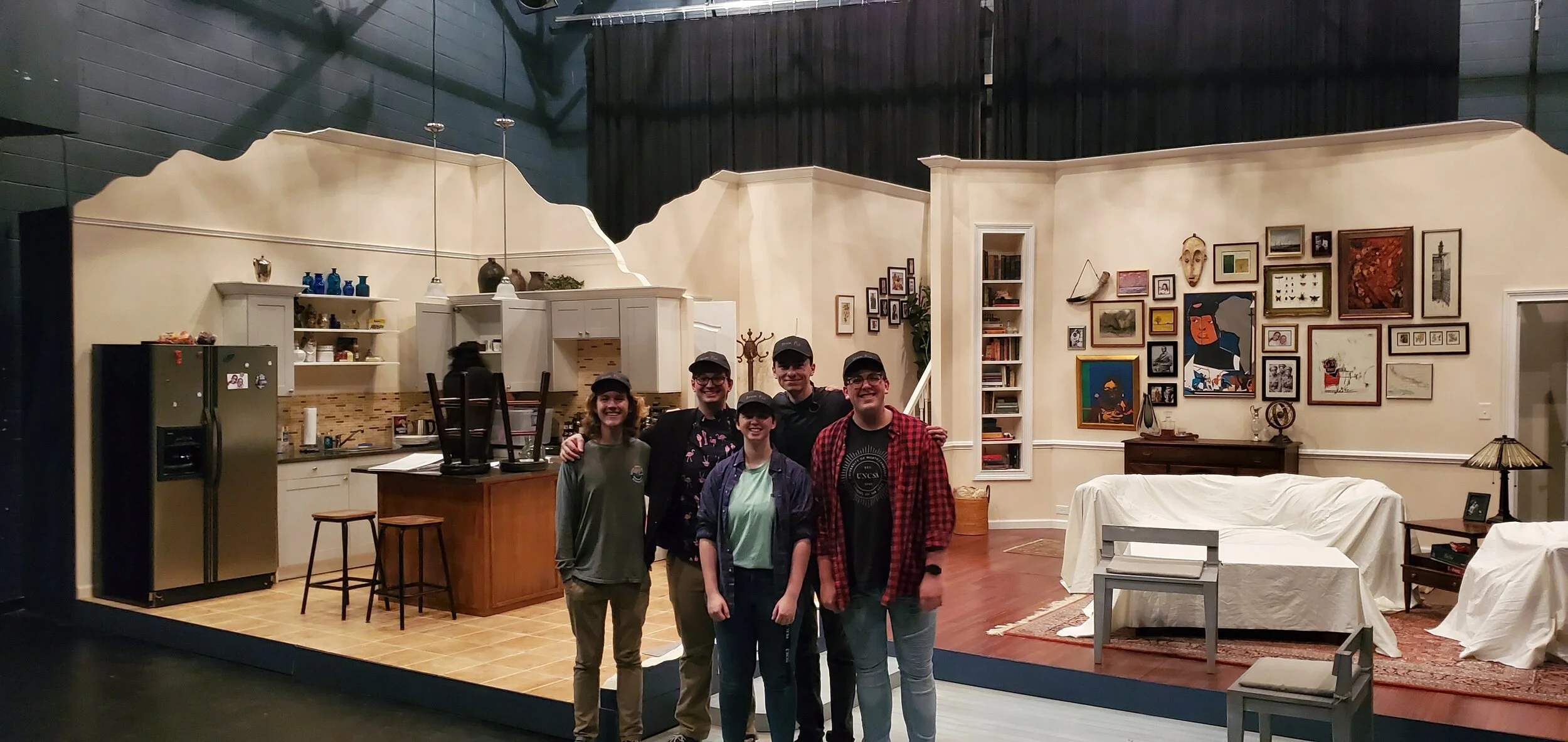